Building your own e-bike battery pack allows you to fully customize it to your bike’s specifications and riding needs. However, the process involves understanding key technical concepts, sourcing high-quality components, assembling cells meticulously, incorporating protective elements, comprehensive testing, and ongoing maintenance best practices. This comprehensive DIY e-bike battery guide covers all vital aspects from how lithium cells work to cost considerations.
Key Takeaways: Building Your Own E-Bike Battery Pack
Takeaway | Summary |
---|---|
Understand Battery Fundamentals | Grasp how lithium-ion cells interconnect in series/parallel to produce needed pack voltage and capacity. |
Source Quality Cells | The right high-grade li-ion cells constitute the most vital component. Evaluate options balancing performance, size, weight and safety. |
Assemble Components Meticulously | Carefully handle cells when welding connectors. Include circuit protection devices like a BMS. |
Test and Validate Functionality | Fully test and break-in new packs across charge cycles monitoring cell balance. |
Incorporate Maintenance Best Practices | Periodically retest cell health. Watch for physical degradation and proactively replace deteriorating cells. |
Always Prioritize Safety | Follow vital precautions when working with lithium cell dangers. Seek help for unfamiliar practices. |
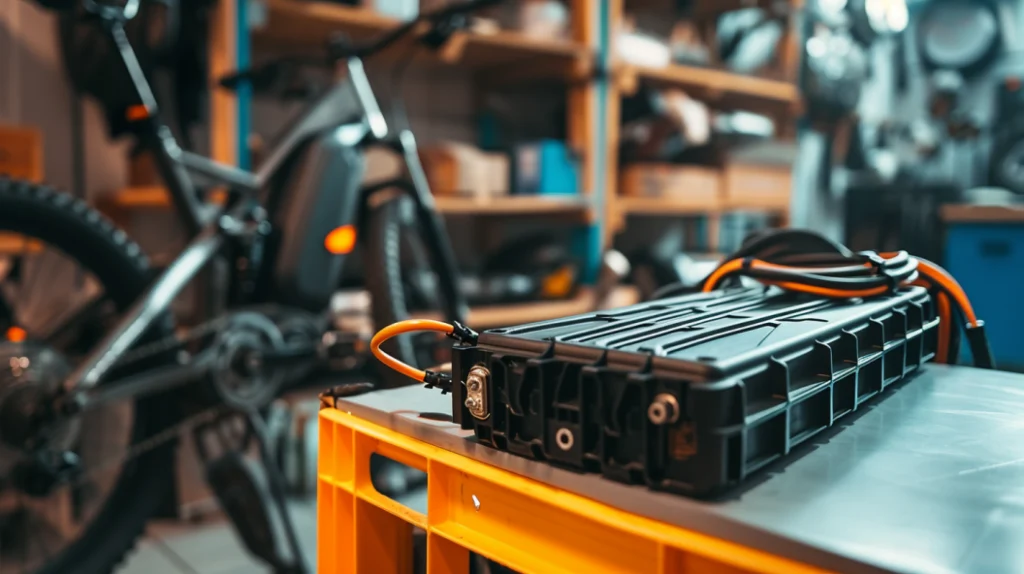
How E-Bike Battery Packs Work
Before constructing a custom pack, grasp how e-bike batteries supply electric power.
Lithium-Ion Cells and Chemistry
Rechargeable lithium-ion cells emerged as the dominant battery chemistry for modern e-bikes given advantageous characteristics:
- High energy density
- Low self-discharge when not in use
- 3.7V cell voltage (higher than alternative chemistries)
- Reduced capacity deterioration over hundreds of charge/discharge cycles
These cells package the active materials in various form factors:
Cell Form Factor | Description |
---|---|
Cylindrical | Literally cylinder shaped, offered by multiple makers |
Pouch | Flexible enclosed flat packs |
Prismatic | Box-shaped cells |
Inside li-ion cells, lithium ions shuttle back and forth between the anode (graphite) and cathode (metal oxide) to induce current flow when powering the e-bike’s drive system.
Connecting Cells For Pack Voltage and Capacity
Individual lithium-ion cells operate at low voltages around 3.7V. Achieving levels usable for e-bike systems requires interconnecting numerous cells in series and parallel configurations.
The total pack voltage relates directly to the number of cells wired in series. More parallel connections enhance the overall battery capacity supporting extended runtimes per charge. Mathematical formulas illustrate the relationships:
Metric | Formula |
---|---|
Total voltage | Number of cells in series * cell voltage |
Total capacity | Number of cells in parallel * cell capacity |
Carefully selecting cell components and architecting series/parallel layouts aims to meet voltage, capacity, weight, and bike integration requirements.
The art in building DIY e-bike packs revolves around optimizing interdependent voltage, capacity, mass and size considerations for intended usage.
Supporting Electronics Regulation
The battery packs interface with sophisticated bike electronics regulating power delivery to the electric motor. Proper steady voltage helps these electronics maximize efficiency and avoid potential damage from voltage spikes.
Incorporating elements like a Battery Management System and supplemental components (fuses, thermistors, contactors) governs charge and discharge within safe bounds for lithium cell longevity.
Choosing the Right Cells
Selecting quality lithium-ion cells constitutes the most pivotal decision when sourcing DIY e-bike battery pack components. Myriad interdependent factors weigh on determining optimal cells.
Voltage and Capacity Requirements
The starting point for cell selection should be confirming your e-bike model’s input voltage range tolerance along with the desired capacity (range per charge). Cross-check specifications to narrow viable cell options.
Higher voltage directly translates into more torque and power from electric drive systems. However, exceeding electronic tolerances risks permanent damage.
Greater battery capacity allows longer rides between charging by storing more onboard energy. But it also increases weight.
Physical Size and Weight Considerations
In addition to the electrochemical performance factors above, the available battery enclosure space and overall e-bike handling depend greatly on physical cell size dimensions, and mass.
Bulkier or heavier cells may overstrain tight spatial constraints and negatively alter frame weight distribution affecting maneuverability.
When possible, opt for the smallest, lightest cells satisfying your pack’s voltage and capacity ceiling to enable flexible positioning while minimizing impacts on ride dynamics. Lower internal resistance also aids efficiency.
Cell Brand and Quality
Lastly, reputable established cell manufacturers adhering to quality assurance processes promote reliable long-term functionality spanning hundreds of charge cycles.
Renowned makers of lithium cells include:
- Panasonic
- Samsung
- Sony
- Sanyo
Conversely, cut-rate cells often cut corners negatively impacting longevity while posing heightened safety risks from potential overheating, fires or explosions. The upfront savings fail to justify assuming such dire consequences.
Key Cell Selection Checklist
Factor | Importance | Ideal Trait |
---|---|---|
Voltage | Matches e-bike system | Within bike’s max tolerance |
Capacity | Supports needed range | As high as required |
Size/Weight | Integrates into frame | As small and light as viable |
Brand | Impacts safety and longevity | Reputable established maker |
Carefully weighing these parameters helps narrow down optimal cells tailored for your e-bike’s particular specifications and intended riding style needs.
Assembling the Battery Pack
With quality lithium-ion cells sourced, the intricate process begins for connecting them into a unified high-performance pack. This requires diligent attention to detail.
Mapping Out Cell Layout
First, map out the full cell array structure and positioning on paper indicating the planned series and parallel connections.
Consider the most efficient shape and orientation filling the enclosure space while allowing sufficient cooling gaps between cells. Verify the series count achieves the target voltage by multiplying the expected cell quantity by the nominal voltage.
Mechanical Cell Joining Methods
Various techniques securely connect li-ion cells mechanically:
Spot welding – The most common technique is spot welding nickel strips between cell terminals. This fuses connections efficiently but demands expensive specialized programmable equipment.
Soldering – Manually soldering wires or tabs also affix cell interconnects. However, extreme localized heat risks damaging cell internals if not practiced carefully.
Battery holders – Plastic snap-on holders provide a solid interface without direct welding or soldering. The modular approach also enables replacing single faulty cells down the line.
Electrical Wiring Considerations
Apply appropriately thick gauge wires between parallel cell groups rated to handle maximum anticipated discharge currents without excessive voltage losses or heat buildup. Keep wire runs physically separated to avert accidental shorts.
Double-check all connections to verify integrity with solid fit and electrical continuity. Insulate exposed high voltage terminals to fully isolate and prevent dangerous accidental contact.
Incorporating Protective Elements
Protecting expensive lithium-ion cells necessitates supplemental components to govern charging and discharging within defined safe parameters. This prevents abusing batteries in ways that could lead to catastrophic thermal runoff or failure.
Battery Management System
A dedicated Battery Management System (BMS) represents the first critical line of defense, continuously monitoring:
- Individual cell voltages
- Cell temperatures
- Total pack current
The BMS actively balances out deviations between cells by shuttling charges as warranted to maintain harmony. If any monitored parameters exceed allowed thresholds, the system can cut off further charging or disconnect the pack entirely.
BMS functionality provides indispensable real-time protection for lithium battery packs.
Select BMS models rated for peak currents at least 20% above maximum anticipated loads.
Supplementary Passive Safety Components
Additional passive devices add further redundancy:
- Fuses – Simple fuses blow open circuits when sensing overcurrent conditions, breaking the flow to prevent thermal cascading.
- Voltage regulator – Regulators clamp voltage spikes from exceeding cell upper limits during regenerative braking energy recovery.
- Thermistor – Negative temperature coefficient (NTC) thermistors reduce current when detecting overheating situations.
- Contactor – An ON/OFF contactor switch manually isolates the pack when not in use as an override line of defense.
Testing and Initial Charging
Upon completing the initial battery pack assembly, comprehensive testing and balancing procedures ensure all cells operate in harmony as intended over multiple cycles:
Voltage and Polarity Verification
Check total pack voltage matches expectations based on cell quantities using a multimeter. Significantly lower readings indicate a bad connection requiring rework.
Compare relative cell voltages when fully saturated. Differences exceeding 50-100 mV between adjacent cells necessitate active or passive balancing to avoid deteriorating performance spreading between mismatched cells.
Passive Balancing Elements
The simplest approach uses passive bleed resistors to dissipate excess voltage variances by bleeding off charge into heat. However, this wastes power versus active electronics shuttling current between cells.
Condition | Action Threshold | Risk |
---|---|---|
Over-voltage | > 4.2V/cell | Thermal runaway |
Under-voltage | < 2.5V/cell | Reverse polarity |
Voltage difference between adjacent cells | > 50-100mV | Imbalance; premature failure |
Initial Charging
Repeat testing over multiple full charge and discharge cycles until cells stabilize with voltages staying balanced within tolerance bands.
Also, check for hot spots or swollen cells indicating potential internal faults to proactively replace suspected bad cells before catastrophic failures arise.
Integration and Validation
Finally, verify the intended functionality when integrated into the e-bike frame before relying on the new pack out on the trails. Consider unintended vibration or environmental issues.
Battery Enclosure Selection and Mounting
The enclosure houses and protects delicate battery components. Material choices and mounting strategy impact longevity.
Enclosure Material Properties
Hard plastic or metal enclosures will shield cells from weather and physical impacts while enabling ventilation to avoid overheating. The enclosure mounts securely to the bike frame using vibration-damping fasteners to maintain stability.
Some DIY builders fashion custom enclosures allowing greater flexibility in marrying form and function using CNC machining or 3D printing.
Key Enclosure Considerations
- Physical protection from debris
- Weather and water resistance
- Material choices – plastic or metal
- Ventilation – airflow gaps
- Secure frame mounting/integration
- Aesthetic preferences
Getting enclosure details right ensures your battery investment stays safe on and off the trails.
Advanced Cell Arrangements
While basic series and parallel cell connections provide a basic battery architecture, more complex arrangements enable highly specialized pack designs.
Cell Segmentation
Partition the pack into multiple segmented cell groups with parallel sub-arrays to meet ultra high capacity requirements. This also raises peak current handling limits compared to fewer strings.
Additional BMS units can steward each defined cluster for enhanced monitoring and balancing. Just take care to evenly distribute discharge loads across all segments.
Cell Nesting
Complex nested groupings mix intricate series and parallel connections to optimize pack shape filling the entire enclosure volume. However, such layouts require meticulous planning to track elaborate wiring runs and balance currents.
Incorporating Regenerative Braking
Regenerative braking technology recovers a portion of kinetic energy during deceleration which charges the battery. This requires accommodating reverse current flows using charge controllers and diodes to avoid damaging sensitive electronics.
Diagnosing Battery Issues
While lithium-ion cells generally prove reliable over hundreds of usage cycles, problems can occasionally arise with aging packs:
Check Individual Cell Voltages
Compare all cell voltages across the pack to pinpoint any outliers indicating bad cells.
Inspect Physical Condition
Examine for potential damage, swollen cases, or degraded terminal connections contributing to faults.
Decode BMS Indicator Codes
Consult BMS console error codes for diagnosing issues if present.
Analyze Performance Trends
Download historical data logs from the BMS showing charge/discharge curves over time to identify deteriorating patterns.
Proactively Replace Cells
Pre-emptively swap out suspect weak or imbalanced cells to restore the entire pack to health rather than premature failures.
Developing a diligent troubleshooting methodology helps maximize your custom battery’s reliable lifetime through timely maintenance.
Strategies for Expanding Pack Capacity
As batteries inevitably age, accumulating charge/discharge cycles take a toll as their internal resistance climbs steadily lowering usable capacity due to increased inefficiency.
To offset dwindling capacity on older packs, periodically augment with supplemental parallel cells to restore range to original as-new levels. Take care to closely match new cells’ specifications to existing ones when combined.
Cost Optimization Fundamentals
DIY e-bike battery builds demand significant upfront monetary and time investments. Seek a reasonable balance between component quality and budget realities.
Prioritize Vital Systems
Allocate limited resources first towards fundamental safety protections like a proper BMS before spending lavishly on premium cells or tools. Used or entry-level gear often suffices for one-off hobbyist builders.
Account For Usage Horizon
Carefully factor long-term usage plans spanning hundreds of future charge cycles to maximize value from initial sunk costs. Purchasing higher-performing components amenable to augmenting later often merits spending slightly more initially.
Conclusion
Constructing DIY e-bike batteries requires understanding how lithium cells functionally wire together to achieve the necessary system voltage and capacity. This depends on the specific e-bike’s power specifications and intended riding usage.
Once equipped with core conceptual knowledge, thoughtfully source the most well-suited battery cells balancing factors like peak output, physical size limitations, mass targets and overall quality and safety considerations. Premium cells constitute the vital heart of high-performing custom packs.
Entrust assembling procedures to meticulously fuse cells, incorporating robust mechanical joints and electrical interconnects. This stage demands exceptional attention to detail along with safety practices when dealing with volatile lithium components. Include supplemental protection electronics like Battery Management Systems which monitor cell health maximizing safe operating lifetimes.
Upon completing initial battery construction, rigorously validate overall functionality under real-world charging and discharging conditions across multiple cycles. This helps identify any potential cell balance issues or faulty components early on before permanent failures occur down the road.
FAQs
Q: Is it legal to build your own e-bike battery pack?
A: In most jurisdictions, it is legal to build your own e-bike battery pack as long as you comply with local regulations and safety standards. It’s important to ensure that the battery pack meets the required voltage and capacity limits and that it is properly installed and maintained.
Q: How long will my custom e-bike battery pack last?
A: The lifespan of an e-bike battery pack depends on several factors, including the quality of the cells, the charging and discharging patterns, and the maintenance of the pack. With proper care and maintenance, a well-built e-bike battery pack can last for several years.
Q: Can I use any type of lithium-ion cells for my e-bike battery pack?
A: It’s important to use high-quality lithium-ion cells from a reputable manufacturer to ensure the safety and performance of your e-bike battery pack. It’s also important to choose cells with the right voltage, capacity, and size to suit your specific requirements.
Q: How can I maximize the range of my e-bike with a custom battery pack?
A: To maximize the range of your e-bike, it’s important to choose high-capacity cells and to balance the cells to ensure that they are operating at their optimal levels. It’s also important to maintain the battery pack and to use efficient e-bike components to minimize energy consumption.
Q: Are there any safety precautions I should take when building my e-bike battery pack?
A: When building your e-bike battery pack, it’s important to take several safety precautions, including using the right tools and equipment, following the manufacturer’s recommendations, and testing and balancing the cells to ensure that they are operating safely. It’s also important to be aware of the risks associated with lithium-ion batteries, such as fire.